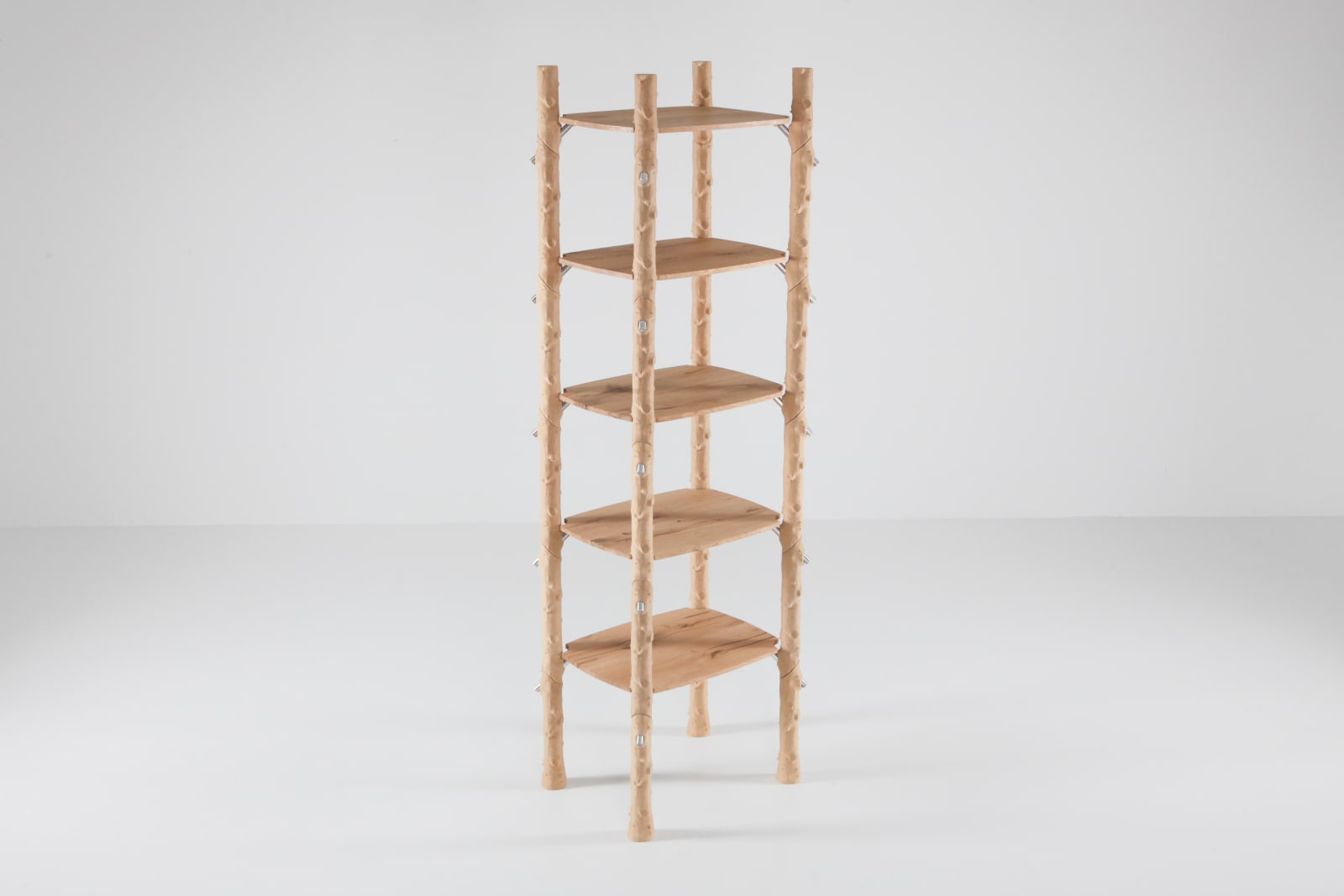
Schimmel & Schweikle Dutch/German, b. 1993/1994
Branch-ish shelf, 2020
White american oak, wood filament, acrylic plaster, pu-foam, aluminium and hardware
H 220 x W 65,5 x D 52,3 cm
Copyright The Artist
At the core of the “Stacked wrinkles shelf” is one reoccurring element that can be found in many pieces of the show; the branch textured prints. Here we took an...
At the core of the “Stacked wrinkles shelf” is one reoccurring element that can be found in many pieces of the show; the branch textured prints. Here we took an image of a natural branch into the 3D modelling software, created a 3D texture out of it which we then printed. To us it was particular interesting how we could re-create a natural structure over which we have full control. The whole shelf is made from 24 identical branch beams. In their totality they appear like a natural structure but when looking closer the digital manufacturing technique becomes clear as you see that the whole structure is made from one repeating element.
In contrast to the natural branch texture stands the very constructive connection of the separate beams. In order to connect them we gave each end of the beam a 45degree angle and connect them with a dowel going through both ends of a beam. This idea of connecting two wooden pieces comes from traditional carpentry were making wood joints is a major way to connect wooden pieces without screws or nails. In this example we like to show how 3D printing can borrow/learn from traditional crafts by adapting concepts of construction. The notches that form around the aluminium tubes make it look like the aluminium tubes have been in there for years and the branch started to grow around the tube. This is another type of natural behaviour that can be simulated by the computer and further blurs the border between computer generated and natural growth. The four pillars are connected with 5 wooden planks made from american white oak. These planks not just structurally connect the prints but also from a conceptual point of view connect the 3d printed beams to their natural origin.
In contrast to the natural branch texture stands the very constructive connection of the separate beams. In order to connect them we gave each end of the beam a 45degree angle and connect them with a dowel going through both ends of a beam. This idea of connecting two wooden pieces comes from traditional carpentry were making wood joints is a major way to connect wooden pieces without screws or nails. In this example we like to show how 3D printing can borrow/learn from traditional crafts by adapting concepts of construction. The notches that form around the aluminium tubes make it look like the aluminium tubes have been in there for years and the branch started to grow around the tube. This is another type of natural behaviour that can be simulated by the computer and further blurs the border between computer generated and natural growth. The four pillars are connected with 5 wooden planks made from american white oak. These planks not just structurally connect the prints but also from a conceptual point of view connect the 3d printed beams to their natural origin.